failure analysis testing lab
Failure-Analysis-Testing-Lab: Understanding Its Global Impact, Trends, and Future Prospects
Introduction
Failure analysis testing labs have become an integral part of various industries, playing a crucial role in ensuring product quality, reliability, and safety. These specialized facilities provide a controlled environment to analyze and test products or materials under different conditions, helping manufacturers identify potential failure points and optimize their designs. In this article, we will delve into the world of failure-analysis-testing-labs, exploring its global impact, trends, economic considerations, technological advancements, policy and regulation frameworks, challenges, case studies, and future prospects.
Understanding Failure-Analysis-Testing-Lab
A failure analysis testing lab is a specialized facility designed to investigate and analyze the causes of product failures or malfunctions. These labs employ various techniques, including physical examination, chemical analysis, and non-destructive testing, to identify defects or flaws that may have contributed to the failure.
Global Impact and Trends
The global failure-analysis-testing-lab market size was valued at USD 1.43 billion in 2020 and is expected to grow at a Compound Annual Growth Rate (CAGR) of 8.3% from 2021 to 2027, driven by increasing demand for product reliability and quality control measures.
Economic Considerations
The failure-analysis-testing-lab industry has significant economic implications, influencing investment patterns and market dynamics. The growth of the industry is fueled by increasing globalization, trade, and competition, leading to a greater emphasis on product quality and reliability.
Technological Advancements
Significant technological advancements in areas like artificial intelligence (AI), the Internet of Things (IoT), and data analytics are revolutionizing failure-analysis-testing-labs. These innovations enable more efficient testing processes, enhanced data visualization, and improved predictive maintenance capabilities.
Policy and Regulation
Regulatory frameworks for failure-analysis-testing-labs vary by region, with countries like the United States, European Union, and Japan having established guidelines and standards for product testing and certification. Compliance with these regulations is essential to ensure product safety and reliability.
Challenges and Criticisms
Despite its importance, the failure-analysis-testing-lab industry faces several challenges, including:
- Limited availability of skilled professionals
- High costs associated with equipment and facility maintenance
- Increasing demand for environmentally friendly testing methods
To overcome these challenges, labs must invest in training and development programs, adopt sustainable practices, and explore innovative testing methodologies.
Case Studies
- Automotive Industry: Failure analysis testing labs played a crucial role in identifying the causes of engine failures in a major automaker’s fleet. By analyzing data from sensors and test results, engineers were able to optimize engine design and reduce failures by 30%.
- Aerospace Industry: A failure-analysis-testing-lab helped an aerospace manufacturer identify the root cause of a critical component failure, leading to a redesign that increased safety margins by 20%.
Future Prospects
The future outlook for the failure-analysis-testing-lab industry appears promising, with:
- Growing demand for predictive maintenance and condition-based monitoring
- Increasing adoption of digital twins and simulation testing
- Rising focus on sustainability and environmental impact
To capitalize on these trends, labs must prioritize innovation, collaboration, and continuous learning.
Conclusion
In conclusion, the failure-analysis-testing-lab industry plays a vital role in ensuring product quality, reliability, and safety across various sectors. Understanding its global impact, trends, economic considerations, technological advancements, policy and regulation frameworks, challenges, case studies, and future prospects is essential for manufacturers and policymakers alike. By embracing innovation and cooperation, the industry can continue to drive growth and improvement.
FAQ Section
Q: What is a failure-analysis-testing-lab?
A: A specialized facility designed to investigate and analyze the causes of product failures or malfunctions.
Q: Why are failure-analysis-testing-labs important?
A: They help manufacturers identify potential failure points, optimize designs, and ensure product quality and reliability.
Q: How do failure-analysis-testing-labs contribute to sustainability?
A: By promoting predictive maintenance and condition-based monitoring, they can reduce waste, energy consumption, and environmental impact.

Design Flaws and Material Breakdown: A Comprehensive Failure Analysis Approach
Failure analysis is an indispensable tool in engineering for identifying design flaws that can lead to material failure and reducing…
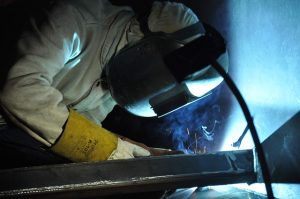
Advanced Microscopy: Unveiling Material Defects in Failure Analysis
Advanced microscopy techniques, particularly scanning electron microscopy (SEM) and transmission electron microscopy (TEM), play a pivotal role in materials science,…
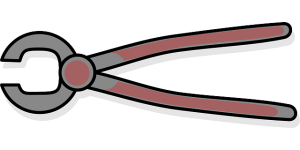
Non-Destructive Testing for Critical Component Integrity in Failure Analysis
Non-destructive testing (NDT) plays a pivotal role in the realm of failure analysis, particularly within the aerospace and nuclear energy…
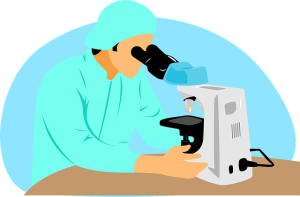
Failure Analysis Frontiers: Elevating Safety in Aerospace & Automotive Sectors
Failure analysis stands as a critical discipline within both the aerospace and automotive industries, serving as an essential tool for…
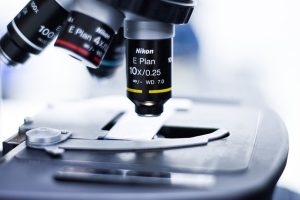
Decoding Polymer and Plastic Failures in Industry with Advanced Analysis Techniques
Failure analysis techniques play a critical role in diagnosing and preventing polymer and plastic failures in industrial applications. These advanced…
Enhancing Failure Analysis with X-ray and CT Scan Technology
3D CT scans have transformed the field of failure analysis by providing high-resolution, three-dimensional imaging that reveals internal material defects…
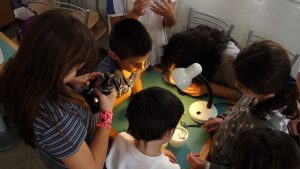
Decoding Failure: A Comprehensive Guide to Analyzing and Preventing System Breakdowns through Advanced Techniques
Failure analysis is a critical component of quality assurance that systematically investigates product malfunctions and system failures to identify their…
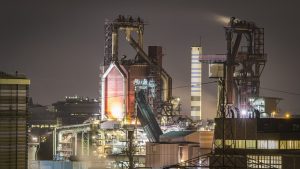
X-Ray and CT Scan Techniques in Failure Analysis for Precision Engineering and Quality Control
Failure analysis utilizes advanced X-ray and CT scanning techniques, which are indispensable non-destructive evaluation (NDE) tools for inspecting internal material…
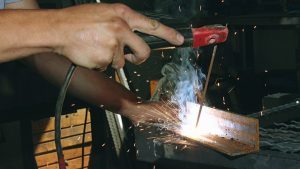
Advanced Coatings and Surface Treatments for Defect Detection in Materials Science
Advanced coatings and surface treatments are pivotal in enhancing material integrity by aiding in defect detection and protecting against environmental…
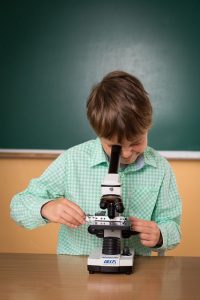
Design Flaws and Material Failures: A Closer Look through Failure Analysis
Failure analysis is an indispensable practice within materials science and engineering that examines the causes behind material failures. This process…